What To Do When Taking Inventory In A Small Business
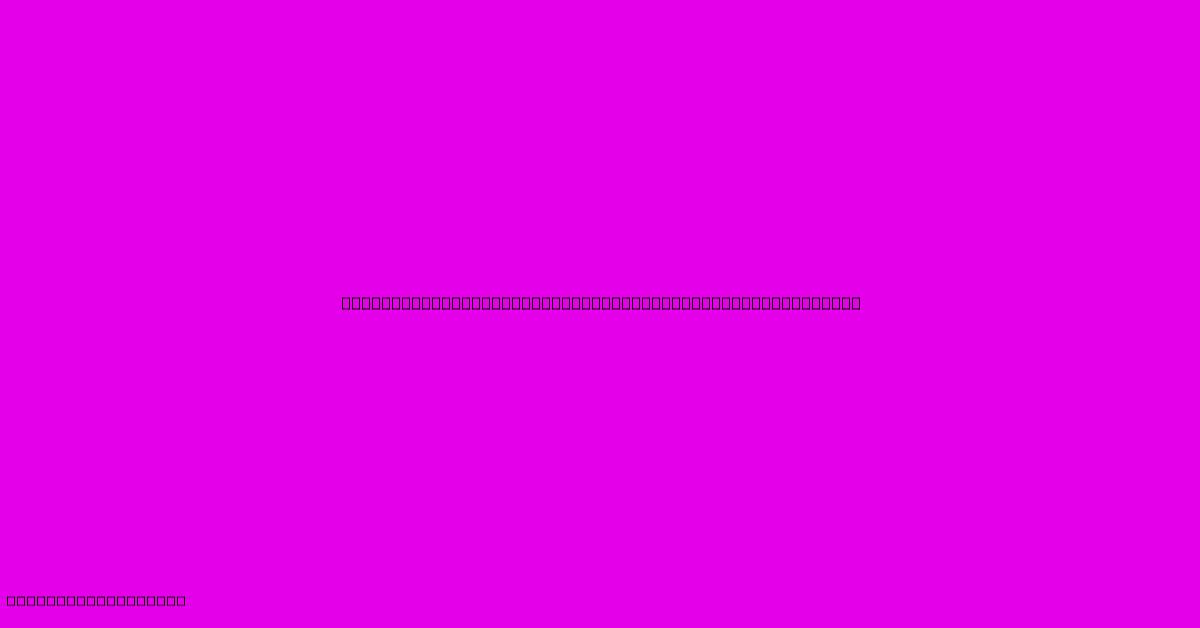
Discover more in-depth information on our site. Click the link below to dive deeper: Visit the Best Website meltwatermedia.ca. Make sure you don’t miss it!
Table of Contents
Mastering Inventory: A Small Business Guide to Accurate Stocktaking
What's the secret to a thriving small business? Precise inventory management is key. Without it, you're sailing blind, risking lost profits, unhappy customers, and even business failure. This comprehensive guide unravels the complexities of taking inventory in a small business, empowering you with actionable strategies for accuracy and efficiency.
Editor's Note: Mastering inventory management has been published today, providing invaluable insights for small business owners.
Importance & Summary: Accurate inventory management is crucial for small businesses. It enables informed purchasing decisions, prevents stockouts and overstocking, streamlines operations, and ultimately boosts profitability. This guide offers a step-by-step approach to conducting efficient and accurate inventory counts, covering methods, tools, and best practices. Topics include planning, counting techniques, data management, and utilizing technology to optimize the process.
Analysis: This guide is based on established inventory management principles, best practices from successful small businesses, and research into efficient stocktaking methodologies. The information presented offers practical, actionable steps to improve inventory accuracy and reduce the time and resources required for the process.
Key Takeaways:
- Plan meticulously before starting.
- Choose the right inventory counting method.
- Utilize technology to streamline the process.
- Implement robust data management systems.
- Regularly review and refine your inventory procedures.
Taking Inventory: A Detailed Walkthrough
Introduction: The process of taking inventory, often referred to as stocktaking, is fundamental to the health of any small business. It involves systematically counting and recording all items in your inventory, ensuring the physical count matches your recorded stock levels. Inaccuracies can lead to significant financial losses, impacting profitability and customer satisfaction.
Key Aspects:
- Planning and Preparation: Thorough planning is paramount.
- Counting Methods: Choosing the appropriate method for your business.
- Data Management: Accurate recording and organization of inventory data.
- Technology Integration: Utilizing software and tools to streamline the process.
- Post-Count Reconciliation: Comparing physical counts against recorded levels.
Planning and Preparation: Laying the Foundation for Success
Introduction: The success of your inventory count hinges on effective planning. Failing to prepare adequately can lead to inaccuracies, inefficiencies, and wasted time.
Facets:
1. Define Scope and Objectives: Clearly outline which items to include in the inventory count. This might include raw materials, work-in-progress, finished goods, and supplies. Define the goals of the count – identifying discrepancies, improving accuracy, or preparing for tax purposes.
2. Schedule and Allocate Resources: Schedule the count during a period of low activity to minimize disruptions. Assemble a team, assigning roles and responsibilities to ensure efficiency. Provide adequate training on counting procedures and data recording.
3. Gather Necessary Supplies: Ensure you have all the necessary tools and supplies – scanners, barcode readers, counting sheets, clipboards, pens, and labels. Consider using carts or baskets for efficient movement of items.
4. Prepare the Inventory Area: Organize the inventory area to facilitate easy access to items. Clear clutter, label shelves, and ensure good lighting. This makes the counting process smoother and reduces errors.
5. Establish a System for Data Recording: Decide on a method for recording inventory data. This could involve manual spreadsheets, using barcode scanners linked to inventory management software, or utilizing mobile inventory apps. Choose a system that aligns with your business’s size and capabilities.
Summary: Meticulous planning is essential for a successful inventory count. By defining objectives, allocating resources, gathering supplies, preparing the area, and establishing a data recording system, you lay the groundwork for a smooth and accurate process. The planning stage directly influences the accuracy and efficiency of subsequent steps.
Counting Methods: Choosing the Right Approach
Introduction: Various methods exist for counting inventory, each suited to different business sizes and complexities. Selecting the appropriate method is crucial for accuracy and efficiency.
Facets:
1. Cycle Counting: A continuous process of counting a small portion of inventory regularly. This helps maintain ongoing accuracy and reduces the burden of a complete count. It's ideal for businesses with high inventory turnover.
2. Periodic (Full) Inventory Count: A comprehensive count of all inventory items at a specific point in time. While time-consuming, it provides a complete snapshot of inventory levels and is often required for financial reporting.
3. Using Barcode Scanners and RFID: Barcode scanners and radio-frequency identification (RFID) tags automate the counting process, speeding up data collection and reducing errors. This is particularly advantageous for businesses with a large number of items.
4. Two-Person Counting Method: One person counts, the other records. This helps reduce errors and improves accountability.
5. Third-Party Inventory Services: Outsourcing the inventory count to a specialized service can free up internal resources and ensure accuracy, particularly beneficial for larger or more complex inventories.
Summary: The choice of inventory counting method depends on factors like inventory size, turnover rate, and resources. Cycle counting provides ongoing accuracy, while periodic counts offer a comprehensive snapshot. Technology integration, such as barcode scanners and RFID, significantly improves efficiency. Outsourcing might be considered for businesses needing specialist expertise. The method chosen directly impacts the overall accuracy and efficiency of the inventory process.
Data Management: Ensuring Accuracy and Accessibility
Introduction: Accurate data management is vital for leveraging the information gathered during inventory counts. A well-structured system ensures readily accessible information for informed decision-making.
Facets:
1. Data Entry and Verification: Ensure accurate and timely data entry into your inventory management system. Implement checks and balances to verify the accuracy of the data entered, comparing against physical counts.
2. Data Organization and Storage: Organize inventory data effectively to facilitate quick retrieval and analysis. Utilize appropriate software or spreadsheets to store and manage inventory data, including item descriptions, quantities, and locations.
3. Data Reporting and Analysis: Generate reports to track inventory levels, identify trends, and assess the efficiency of inventory management. Analyze data to detect discrepancies, optimize stock levels, and improve forecasting.
4. Data Security and Backup: Protect inventory data from loss or unauthorized access. Regularly back up inventory data to prevent data loss.
Summary: Robust data management ensures that inventory data is accurate, accessible, and secure. Effective data entry, organization, reporting, and security measures contribute to informed decision-making and efficient inventory control. This is crucial for effective planning and business continuity.
Technology Integration: Streamlining Inventory Management
Introduction: Technology plays a significant role in improving the efficiency and accuracy of inventory management. Leveraging suitable tools can significantly reduce manual effort and increase precision.
Further Analysis: Inventory management software provides numerous benefits, including automated counting, real-time tracking, demand forecasting, and reporting. Barcode scanners and RFID technology offer efficient item tracking and data capture. Cloud-based solutions offer data accessibility from multiple locations.
Closing: Integrating technology into your inventory management process is crucial for staying competitive. The use of appropriate tools enhances efficiency, reduces errors, and improves decision-making. Investing in technology yields long-term benefits in terms of time savings and enhanced accuracy.
FAQ
Introduction: This section addresses frequently asked questions related to taking inventory in a small business.
Questions:
-
Q: How often should I take inventory? A: The frequency depends on your business’s needs and inventory turnover. Some businesses perform a full count annually, while others use cycle counting more regularly.
-
Q: What if I find discrepancies between my physical count and recorded levels? A: Investigate the discrepancies. Check for errors in data entry, theft, damage, or misplacement of items. Adjust your records accordingly and implement measures to prevent future discrepancies.
-
Q: What is the best inventory management software for small businesses? A: Numerous options exist. Consider your business’s specific needs and budget when selecting software. Research reviews and compare features to find the best fit.
-
Q: How can I reduce errors during inventory counting? A: Use a systematic approach, train your team thoroughly, employ double-checking, and use technology like barcode scanners to minimize errors.
-
Q: Can I use a spreadsheet for inventory management? A: Spreadsheets can be used, particularly for small businesses, but dedicated inventory management software often offers more features and automation.
-
Q: What are the consequences of inaccurate inventory management? A: Inaccurate inventory can lead to stockouts, lost sales, overstocking, increased storage costs, and ultimately reduced profitability.
Summary: Addressing these FAQs provides clarity and helps businesses navigate common challenges associated with inventory management.
Tips for Efficient Inventory Management
Introduction: These tips offer actionable strategies for streamlining the inventory management process.
Tips:
-
Implement a robust inventory management system: Choosing the right software or system can make a huge difference in accuracy and efficiency.
-
Utilize barcode or RFID technology: Automating data collection saves significant time and reduces errors.
-
Regularly conduct cycle counts: This minimizes the impact of a complete inventory count and aids in early detection of discrepancies.
-
Train your staff properly: Ensure your team understands inventory procedures, reducing errors and improving overall efficiency.
-
Conduct regular audits: Periodically review your inventory processes to identify areas for improvement.
-
Maintain a clean and organized warehouse: Good organization facilitates easy access and reduces the risk of miscounting.
-
Use a first-in, first-out (FIFO) system: FIFO minimizes the risk of spoilage and ensures that older inventory is used first.
-
Regularly review your inventory levels: This helps to prevent stockouts and overstocking, optimizing inventory levels for your business needs.
Summary: These tips, when implemented, contribute to a more efficient and accurate inventory management process, ultimately leading to improved profitability and business success.
Summary: Mastering Inventory Control
Summary: This guide provided a detailed walkthrough of efficient inventory management in a small business. Key aspects include planning, choosing appropriate counting methods, using technology, and implementing robust data management systems. The provided tips and FAQs offer practical tools to improve accuracy, reduce errors, and optimize processes.
Closing Message: Accurate inventory management is a cornerstone of success for any small business. By implementing the strategies and techniques outlined in this guide, businesses can transform their inventory management processes, reducing costs, improving efficiency, and ultimately boosting profitability. Embrace these strategies and navigate the complexities of inventory control with confidence.
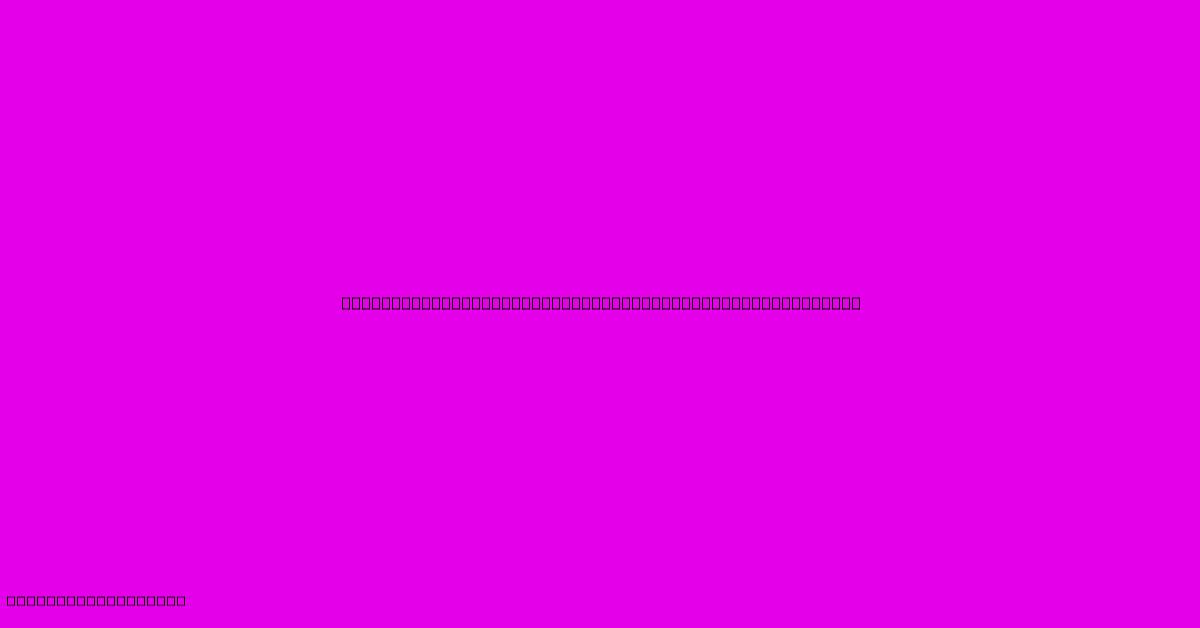
Thank you for taking the time to explore our website What To Do When Taking Inventory In A Small Business. We hope you find the information useful. Feel free to contact us for any questions, and don’t forget to bookmark us for future visits!
We truly appreciate your visit to explore more about What To Do When Taking Inventory In A Small Business. Let us know if you need further assistance. Be sure to bookmark this site and visit us again soon!
Featured Posts
-
Where To Get An Ultrasound Without Insurance
Jan 07, 2025
-
Fiscal Deficit Definition And History In The U S
Jan 07, 2025
-
How To Keep Records For A Small Business
Jan 07, 2025
-
Ballot Definition
Jan 07, 2025
-
What States Accept Electronic Insurance Cards
Jan 07, 2025